Intarsia Yves Laforest
Wood, nature's gift

INTARSIA
What is intarsia? A simple answer: it's like stained glass, but with wood... Personally, I first saw intarsia at an exhibition of La Foire du Bois at St- Hyacinthe. I bought (among other things) a book about making wooden padlocks. This book cost me over $4,000.00 ! It came with a table saw, a planer, a thickness planer, a scrollsaw, a press drill, two sanders and a lot of wood !
The way a piece of intarsia is made will vary a little from one craftsman to another. Here's how I do it, in 6 steps:
Let's see those steps in more detail.
Wood choice
In my intarsia pieces, no stains or paints are used. The colors will be chosen according to the different wood species; white, red, brown, orange, mauve, etc. Currently, I work with around thirty different species.
Next, I look at the texture of the wood. If I want a lined (or ribbed) appearance, with dots (piqué), waves (curly), with reflections, etc., I can choose a wood species that will offer this kind of detail.
You can see some examples below. To see a lot more, you can go to the site of the St-Eustache exotic wood store www.bois-exotique.com) or Ottawa KJP Hardwood (https://kjpselecthardwoods.com).









Parts cutting
Once the essences have been chosen, we move on to cutting. Personally, I start with a plan on paper from which I cut out each piece. Then I glue each piece using a temporary glue (much like Post-It) on a piece of wood and I cut it out using a scroll saw. This is a saw that uses very thin blades which allow you to cut very precisely. The saw I use is an Excalibur with 30 inch throat; that means I can carve parts up to 29 inches in length from it. 29 inches is not that long when making big parts.
In some cases, when the workpiece is long and the cutout is relatively straight, I will also use the bandsaw. Since it cuts much faster, it saves time but you lose a bit in precision.
From beginning to end, I have to make sure that all the pieces fit together as perfectly as possible.

Shaping sanding
The pieces are cut out. Excellent. We now have a "flat" piece which has no relief. At this stage, the piece is not of great interest… Using a belt sanding machine (opposite) with a fairly agressive sand paper, I will sand the piece to give it the relief I want to have; I'm going to make a dent here, give an angle there, etc. After this, the piece will be three dimensional.
In the example below, we can see the wolf head before shaping (left) and after this step (right)

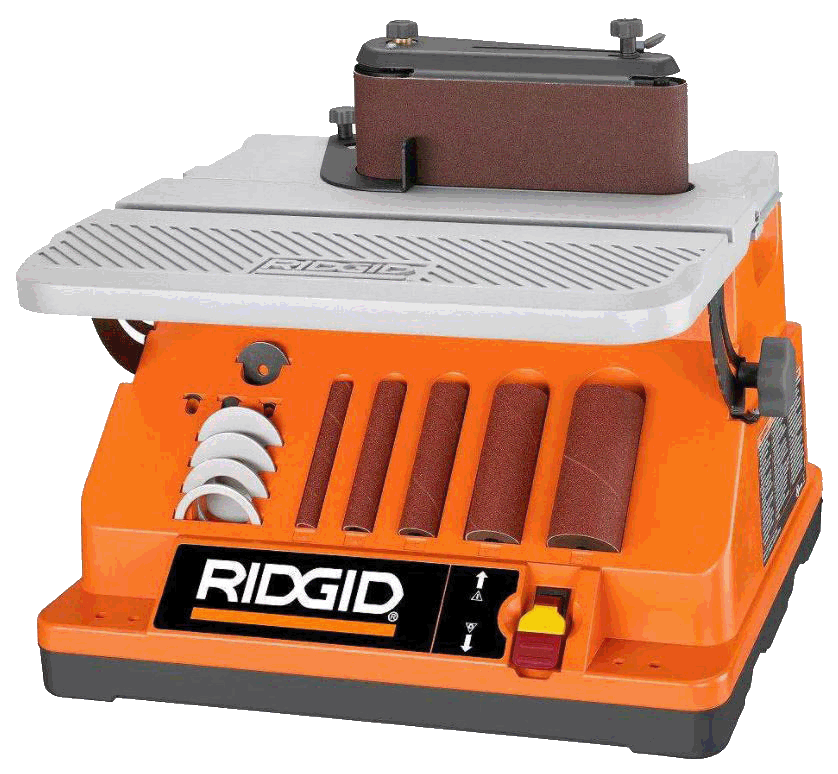
Finish sanding
During the shaping sanding, I used a fairly aggressive sand paper which removes a lot of wood but also leaves a lot of streaks in the wood.
At this point I will go to the sandblaster which uses a pneumatic cylinder with fine sandpaper sleeve mounted on it. Gradually, I will sand to remove the streaks and give the piece a silky appearance.

Assembly
Finally, all the parts have been cut and sanded. The assembly process is a fairly simple step but it still requires precision so that everything fits together perfectly.
I cut a piece of very thin plywood or "lauan" which will serve as backing. I glue all the parts there, hold them in place with metal weights and let everything dry for 5 or 6 hours. Then I go back to the scroll saw to cut out the backing piece following the outline of the piece and then go to the router table to make a 45 degree finish cut. Sand the outline and the piece is ready for finishing.


Final step
Like a large percentage of craftsmen who work with wood, this is the step that I like the least...
Personally, I finish the piece by spraying a few coats of lacquer with a light sanding between each layer. This gives a nice, slightly glossy finish.
After adding a hook and placing a groove on the back, the piece is ready to go to the wall! Et voilà!

Comment?
Would you like to leave us a comment? We will be happy to read it! Simply click here.
Thank you.